In the era of Industry 4.0, data has become a crucial factor driving production efficiency across all industries, including automotive leader in the engineering and manufacturing of advanced suspension and brake systems, BWI Group leverages the power of data analytics to optimize manufacturing processes, increase efficiency and deliver quality and price optimized components to its customers.
Challenges of today’s automotive component manufacturing
Today’s automotive industry exposes manufacturers to unprecedented challenges. The growing pressure to reduce cost while maintaining the highest standards of quality and safety requires innovative approaches to production management. The ability to quickly process and analyze the massive amounts of data generated by modern production lines is key to meeting these challenges. Properly “cleaned” and processed data has the potential to be converted into decision-making processes that lead to actions, contributing to the improvement of quality, efficiency, and reliability of production lines.
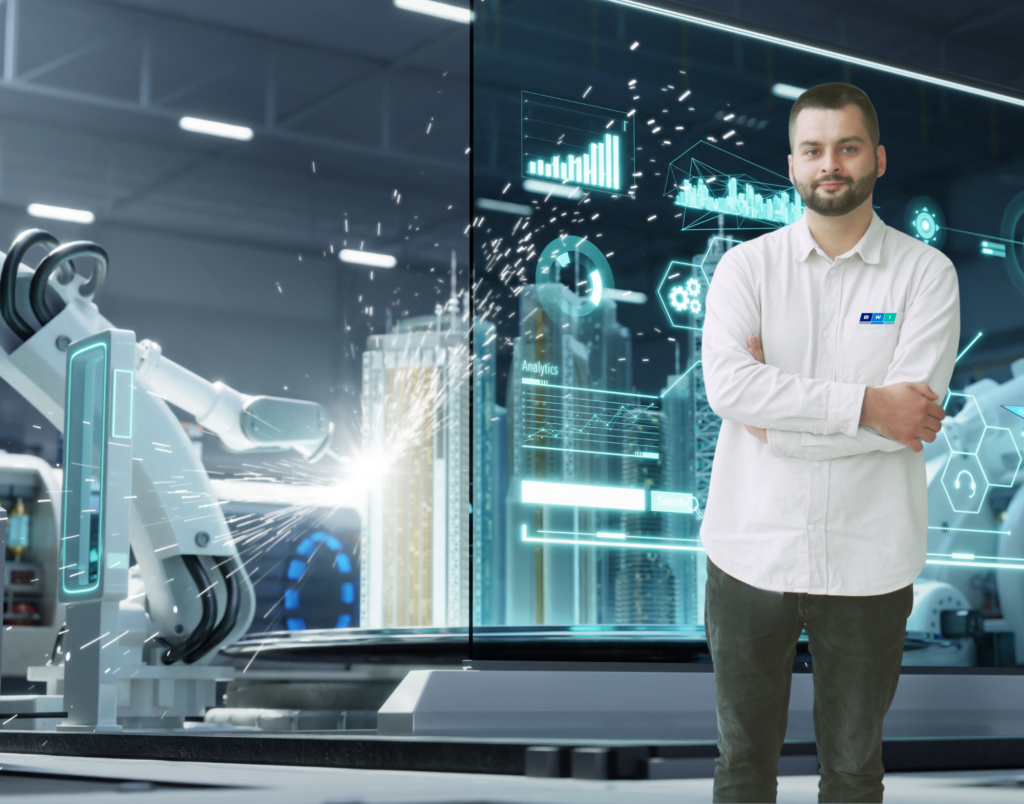
Production Data Management at BWI Group
At BWI Group, we are using a data analytics system developed by the Operational Technology Engineering team, which is based on advanced tools to efficiently and reliably manage information from the manufacturing process. With our system, we achieve:
- Real-time monitoring of Production Line Performance metrics.
This includes identifying the causes of downtime, quality issues, and performance and availability losses. The OPC (Open Platform Communications) systems are used for data acquisition from machine controllers and automation equipment, providing precise and up-to-date insight into production processes. All events are automatically reported, minimizing the need for manual data entry and reducing the risk of errors. Additionally, the data for subsequent analyses is sourced from Single Point of Truth, ensuring a consistent and reliable foundation for continuous improvement and decision making processes in production environment.
- A cohesive Global Information Management Ecosystem for continuous improvement.
This includes a continuous improvement process, managing suggestions and building on lessons learned. BWI uses the Daily Management System to manage tasks and coordinate actions, allowing for effective monitoring of progress and the implementation of corrective actions. Since the environment is consistent with what is used at all levels of the organization, data flows in an organized manner without loss of information.
- An environment for converting production data into specific operational activities.
This ensures an integral and reliable flow of information. Data is processed in a hybrid model both in the cloud and using internal server capacity, improving scalability and security in information management. The solution supports the entire process from problem identification on the production line, through the implementation of corrective actions, to sharing the acquired information with other plants.
- Visualization of Key Performance Indicators (KPIs) on intuitive dashboards created in BI-class systems.
These dashboards are optimized for different organizational roles and offer various levels of detail, enabling quick and easy analysis of key data and decision-making based on current information.
This advanced approach allows for effective production management, process optimization, and quick response to changing conditions, ultimately contributing to the increased efficiency and quality of BWI products.
Customer Centered – The Customer comes first
Improving processes through the deployment of advanced data analytics results in the single most important end outcome, which is the satisfaction of our customers. Let’s list a few of the many benefits:
- Improving product quality by monitoring performance indicators: Quickly detect and eliminate defects, leading to lower defect rates and higher quality of final products.
- Increased production efficiency: Automating the data collection and analysis process helps to detect downtime and other production issues, resulting in faster delivery time and lower operating cost.
- Faster innovation: Data analysis enables dynamic implementation of improvements that meet market needs
,and introduction of new technologies into products. - Increased transparency and better communication: With data visualizations customers have a better insight into production processes and can make faster decisions based on current information.
- Scalability and data security: Using modern cloud technology combined with in-house server resources ensures that systems remain stable and secure even when the amount of processed data increases.
News
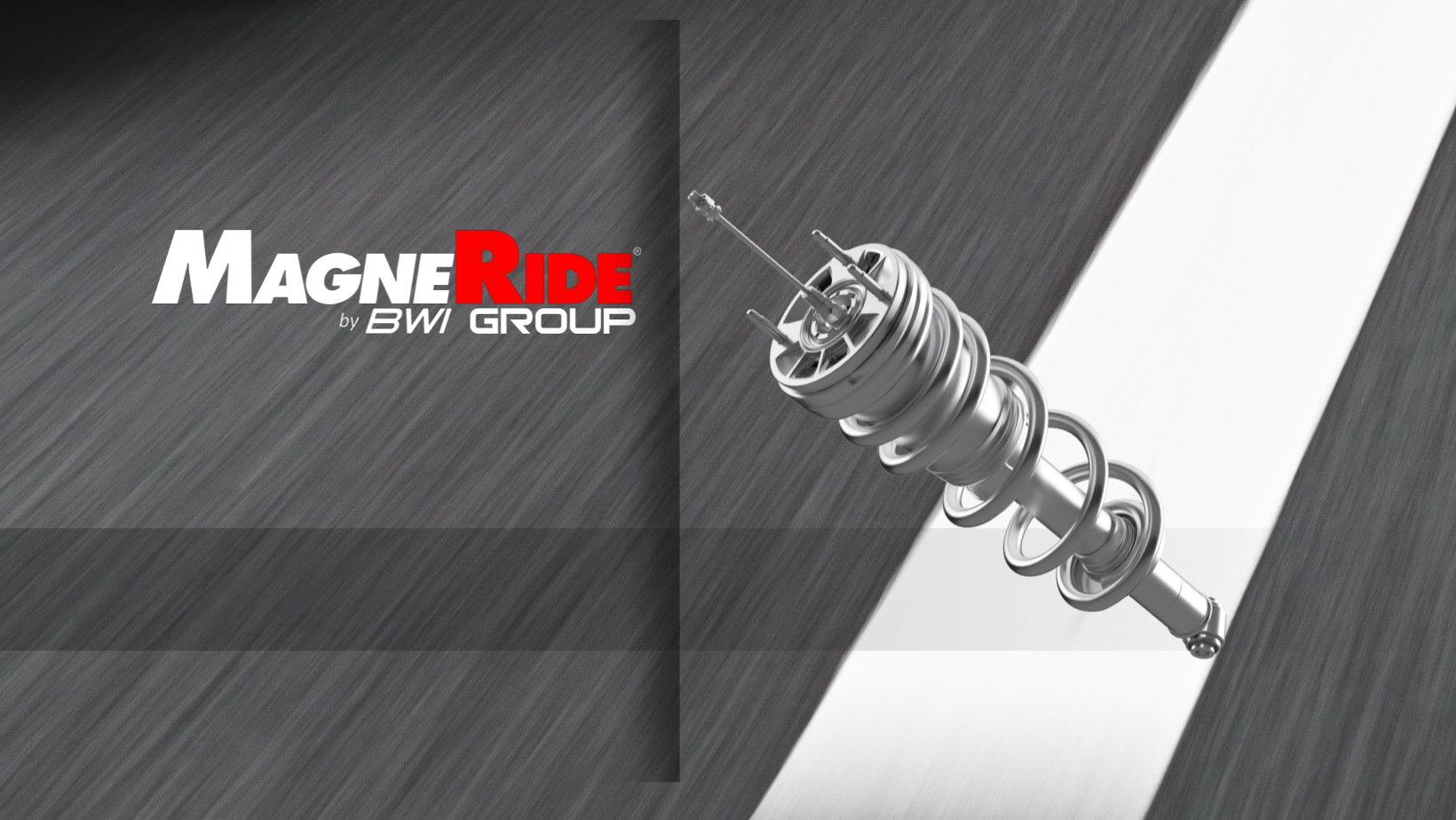
“We’ve introduced several important technological updates to suit the changing requirements of the industry”- says Philippe Germain
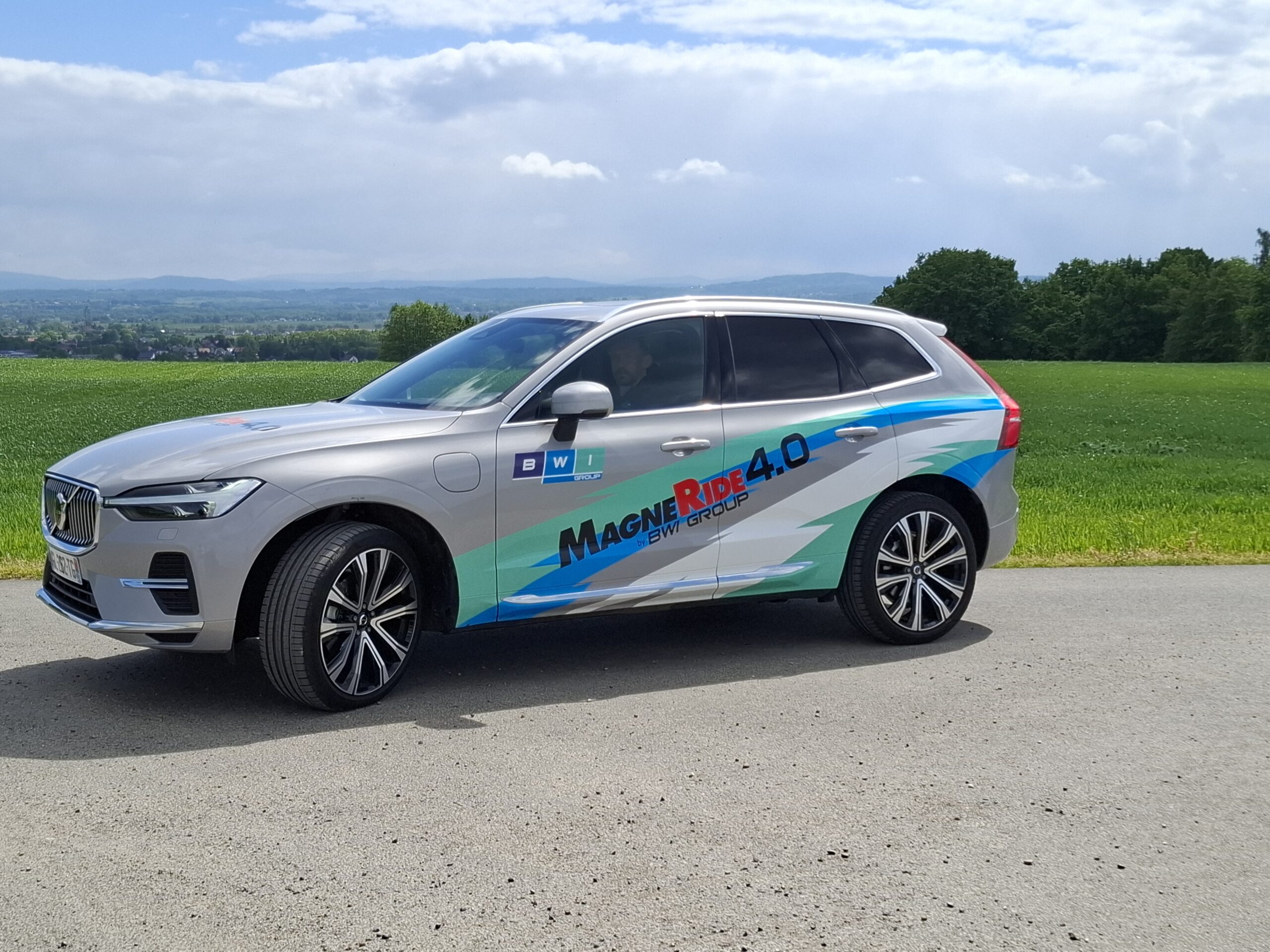
Top suspension technology, BWI MagneRide, more accessible than ever
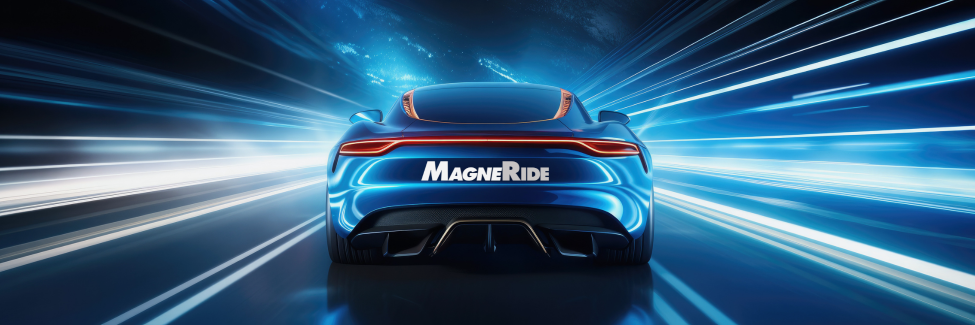